Space Flight Hardware: Keeping the X Rays Cool (Parts I and II)
by Russell Hall, SSEC Publications
Building space flight hardware sounds pretty glamorous to a lot of us: working with state-of-the-art equipment to create instruments that will fly in outer space, enhancing humankind’s understanding of the universe. But when you get down to the nitty gritty reality, it can be far less glamorous.
Ask Tony Wendricks about spending an evening in a Chicago motel room spreading wires so they could be properly plated. Ask Dave Jones about threading those same wires, 1600 of them, one by one through a tiny grid.
Tony and Dave are down in the trenches of an engineering project that will fly on a satellite gathering information about X rays from outer space. They’re building a high-tech refrigerator of sorts to keep detectors working at peak efficiency.
Don’t Say Impossible
The project has been daunting from the start. When the group, which also includes Mike Dean and Mark Mulligan, first met with the Principal Investigator, Dan McCammon of the Physics Department, Tony says his first thoughts were “can we even do this?” The refrigerator uses a magnetic field and salt crystals to supercool gold wires. 1600 gold wires had to be strung, without touching, in a container the size of a soda can. “In the spirit of this place [SSEC],” Tony continues, “I wasn’t going to say it was impossible.”
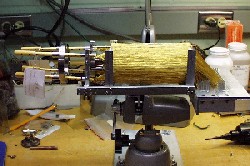
The magnetic salt-crystal cooling element (ADR) under construction. The 1600 gold wires are exposed while they are strung and connected to the four copper rods that will cool one of the Astro-E satellite’s X-ray detectors.
The task for SSEC’s Space Flight Hardware group was to build an Adiabatic Demagnetization Refrigerator (ADR). This small unit will fly on the Astro-E satellite, a joint Japanese-NASA X-ray astronomy project. The ADR will be used to cool one of the satellite’s X-ray detectors down to almost absolute zero. By keeping the temperature low, the heat generated by a single X-ray photon can be detected and measured. Gathering information about X rays will tell us more about things like black holes, white dwarves, supernovae, and a myriad of other far-flung phenomena.
After much trial and error, the team finally hit on a way to string the wires using a perforated disk, which looks more than anything else like a piece cut from a colander with very small holes. The other major component of the project was developing the method to be used for growing the salt crystals. The salt solution includes sulfuric acid and is highly corrosive, forcing the use of some rather expensive materials for the rest of the ADR’s components. Only gold, along with stainless steel, isn’t eaten by the caustic soup used to grow the crystals.
Part II
A Plate of Overcooked Pasta
By manipulating the magnetic alignment of the salt crystal molecules with a large magnet, the ADR can cool to extremely low temperatures. Connected to the crystals using gold wire and gold-plated rods, the detector is cooled to the required temperature of 0.065 Kelvin.
Like every complicated engineering task, there were plenty of problems to overcome. For example, the $4000 spool of gold wire purchased for the project didn’t have nearly the conductivity needed. The solution was to heat and cool the wires in a process called annealing. Again, trial and especially error reared their ugly heads. The first try at annealing, using too high a temperature, resulted in the clumping of wires. As Dave describes it, “They stuck together like a plate of overcooked spaghetti.” Gold wire isn’t the kind of thing that just gets pitched, so Tony and Dave painstakingly peeled the strands apart using tweezers. The second try at 425°C proved to be much more successful.
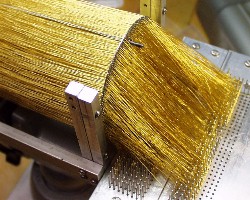
A close-up of the gold wire strung through one of the ADR’s perforated disks. The roll of wire for the project cost $4000.
An Unexpected Layover
The next step was to silver solder four bunches of the wire to the copper rods that will attach to the detector. Because these joints would be exposed to the salt crystals, they had to be gold plated. To get this rather specialized task done, Tony headed off to Chicago. Upon arriving, the plating technicians informed him that the wires were bunched too tightly; in order for the plating to cover the required parts, the wires had to be spread out so that the gold plating solution could flow down between them. Tony spent the better part of an evening in a Chicago motel room spreading 1600 wires so they could be properly plated.
Back in Madison, the ADR had to have its wires installed. “Threading 1600 needles … twice,” Dave says as he explains the stringing of the gold wires. Once again using a tweezers, Dave strung the wires between two disks in the tiny unit.
Dumping Gunk in the Can
Dave and Tony have literally been working around the clock to grow the salt crystals. They have to do “pours” four times a day, which means that Dave has to be in before 6:00 a.m. and Tony has to leave after 12:00 midnight. At each pour, they dump small amount of a solution of ground salt crystals and sulfuric acid into the ADR “can,” as the gold-plated cylinder is indelicately called. The solid pack of crystals (known as a salt pill) is built up two to three millimeters at a time. They hope to be done in 7-14 days.
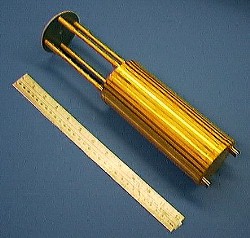
The ADR shown next to a 12-inch ruler. The stripes on the cylinder are alternating rows of gold plate and stainless steel.
As Dave uses a homemade miniature flexible flashlight to peer into the ADR’s small opening to check the progress of the steadily growing salt crystals, Project Manager Bob Paulos sticks his head in. “As you can see, we don’t know what we’re doing,” he jokes. This obvious untruth is met with chuckles from Tony and Dave. It’s obviously been a learning process from the start, but all involved can certainly say that now they DO know what they’re doing.
Once the salt pill is complete, the ADR heads across campus for further testing at Space Physics and then on to NASA’s Goddard Space Flight Center for even more testing. Eventually, it’ll end up in Japan where the launch of the Astro-E is planned for the year 2000. Out in space, Tony and Dave’s sweat and toil will keep the detector operating smoothly for at least two years, gathering information on those elusive X rays. When thought of like that, it lends a certain credence to Tony’s appraisal of the project: “Dave did the impossible.” Just remember, it wasn’t only Dave.